Dexory is a pioneering company in warehouse automation, delivering real-time visibility through autonomous robots and AI-driven analytics. Its towering data capturing robots, extending up to 45 feet tall, autonomously navigate warehouse aisles, scanning tens of thousands of pallet locations and creating digital twins of inventory in real time. This innovation empowers warehouse operators to know exactly what they have and where it is at any moment, dramatically reducing errors and improving efficiency.
However, managing a global fleet of robots across customer sites introduced complex networking challenges. Matthew MacLeod, VP of Software Systems at Dexory, describes how the team adopted Tailscale to achieve secure, seamless connectivity for their robots – without the headaches of traditional VPNs or network tweaks.
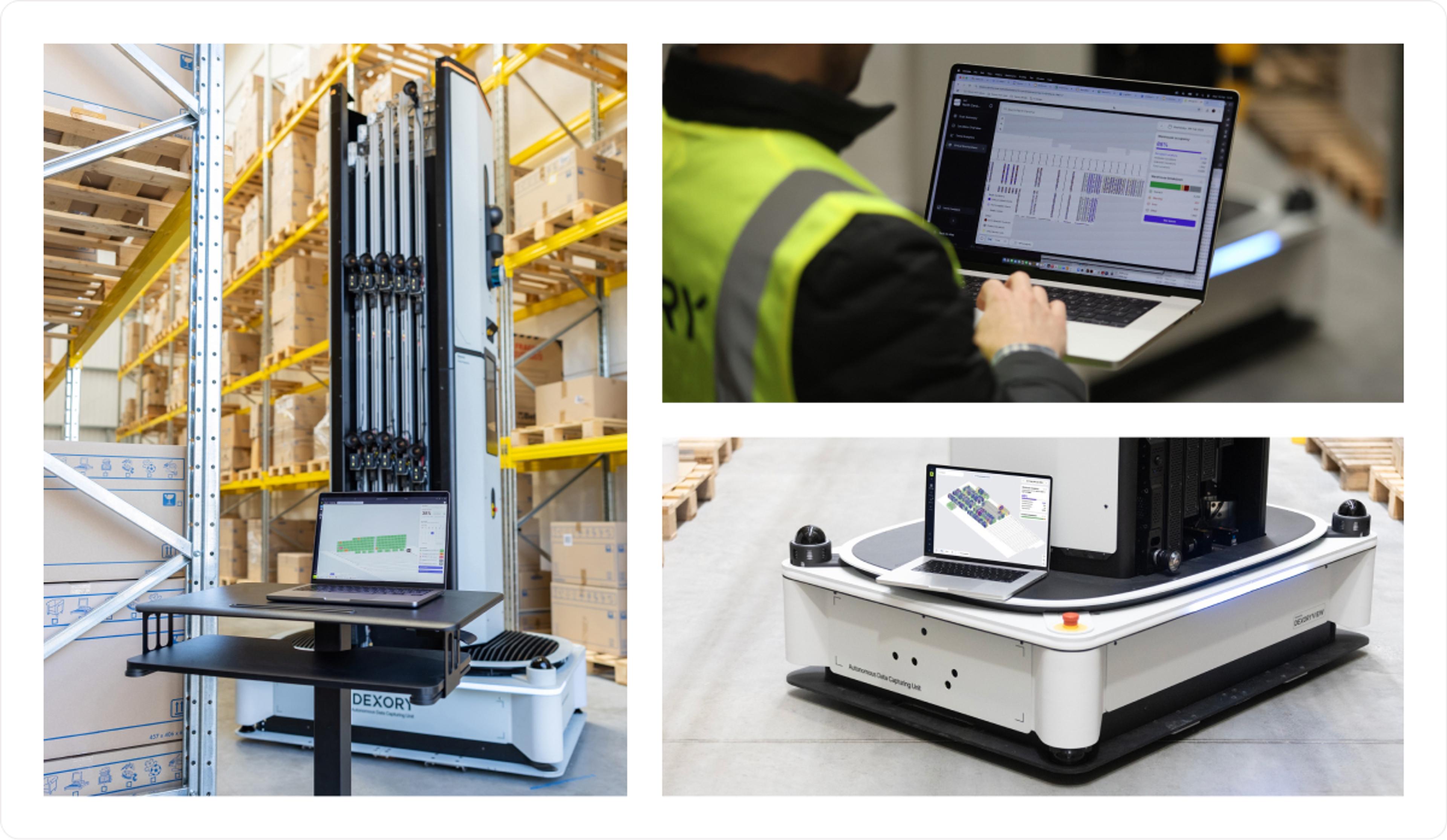
Navigating messy networks at the edge
Each Dexory robot is more than a single device; it’s effectively a moving network of sensors, cameras, and onboard computers. Connecting these robots deployed in warehouses around the world meant dealing with messy networks, overlapping IPaddresses, double NAT, and strict firewalls. Many warehouse IT environments reuse similar private IP ranges and block incoming connections, making it impractical to rely on conventional site-to-site VPNs. “We had no interest in maintaining a custom WireGuard implementation to handle subnet overlaps,” Matthew noted, underscoring that the hidden operational cost of bespoke networking would be tremendous. At the same time, Dexory’s robots needed low-latency, reliable access to send data and receive updates. Their engineers needed to securely reach any robot and its embedded devices from anywhere, without punching holes in firewalls, juggling port forwarding, or redesigning customer networks. In short, Dexory required a secure mesh networking approach built for the complexities of edge deployments.
Embracing a Zero Trust mesh for global robotics
Dexory’s team turned to Tailscale for an elegant solution. From day one, Tailscale’s identity-based mesh VPN delivered connectivity that just works over any internet link, whether a warehouse’s corporate Wi-Fi or a robot’s cellular modem on LTE/5G. The key was Tailscale’s new 4via6 subnet routing capability, which proved to be a game-changer for Dexory’s use case. Robots often use identical IP ranges, but this feature extends Tailscale’s mesh to encompass entire subnetworks, giving each robot’s internal network a unique, unambiguous addressing scheme. In practice, Dexory deploys a lightweight Tailscale agent on each robot’s main computer, which acts as a 4via6 subnet router for the robot’s onboard devices. Now, every sensor or camera on a robot can be reached securely through the Tailscale mesh, without conflicts in IP addresses.
The Dexory team no longer worries about overlapping 10.0.0.0/8 subnets or clashing device IPs – Tailscale transparently maps each one into a unique IPv6 space behind the scenes.
“Tailscale and 4via6 give us secure, low-latency access to our global fleet of autonomous robots - and critically, they make it easy to include embedded networked devices in the same mesh. That flexibility lets us deliver real-time, AI-powered insights to warehouse operators without the overhead of complex VPN or SD-WAN setups”
Simple, secure connectivity for every device
With Tailscale in place, Dexory’s robots and their peripherals are all part of a single protected network, regardless of where they’re deployed. Bringing a new robot online is as straightforward as installing Tailscale on its controller and authenticating it to Dexory’s tailnet. Immediately, that robot appears on the network and is accessible to authorized Dexory services and engineers.
Thanks to 4via6, even devices that cannot run a Tailscale client, like IP cameras or legacy sensors, are reachable. For example, each robot might have a front camera at an internal address of 10.10.0.2 and a rear camera at 10.10.0.3. Ordinarily, having identical IPs on multiple robots would be a networking nightmare. Tailscale assigns every robot subnet a unique identifier, so these addresses are accessed via a distinct domain name or IPv6 route. An engineer can simply use the device’s MagicDNS name (for instance, robot7.dexory.ts.net) or stable Tailscale IP to reach that specific camera on a specific robot, securely over the internet. There’s no need for static public IPs or complicated NAT traversal tricks – Tailscale handles it automatically with end-to-end encryption and peer-to-peer connectivity where possible.
Crucially, this setup is highly secure by design. Every Tailscale node in Dexory’s fleet authenticates using the company’s SSO identity provider, and all traffic is encrypted with WireGuard. Dexory defines fine-grained ACLs (Access Control Lists) to ensure that only the right services and team members can reach sensitive endpoints on the robots. For instance, the warehouse operators get their insights through Dexory’s cloud platform, but only Dexory’s internal systems and engineers have direct network access to the robot’s maintenance ports.
By leveraging Tailscale’s ACL policy, Dexory achieved a Zero Trust network posture. Even though all devices are connected on one mesh, each connection attempt is governed by who, or what service, is allowed to talk to which device. This means unprecedented access control and security oversight compared to the old approach of flat VPN access or open networks.
Efficiency and ease over complexity
Adopting Tailscale has also boosted Dexory’s operational efficiency. The networking overhead for new deployments is practically zero – there’s no need to configure new VPN gateways at each site or maintain an SD-WAN appliance. Tailscale’s lightweight client is deployed as part of Dexory’s standard robot software build, so onboarding a new robot is plug-and-play.
Updates and maintenance are easier too. The Dexory team can push software updates or retrieve logs from robots in the field without leaving their desks, simply by connecting over Tailscale. And because Tailscale’s mesh is resilient with seamless NAT traversal and relaying if needed, the connectivity is more reliable than any custom solution they tried before.
In MacLeod’s experience, the low latency of direct peer-to-peer connections means Dexory can stream data from robots to the cloud in real time, which is vital for their AI analytics. Meanwhile, built-in key management and automatic device key rotation in Tailscale remove the burden of manually managing credentials for thousands of endpoints. All of these benefits add up to more time for Dexory’s engineers to focus on innovation, rather than wrestling with network tunnels and firewalls.
Real-time insights, delivered securely (and effortlessly)
By switching to Tailscale, Dexory gained a secure, low-maintenance network fabric that ties together their globally distributed robots, cloud services, and support engineers. What began as a hunt for a better VPN evolved into a full-fledged connectivity platform for Dexory’s product.
Today, Tailscale’s mesh enables Dexory to deliver AI-powered insights from the warehouse floor to the cloud in real time, without compromising on security or performance. The company avoided the cost and complexity of traditional solutions: “We’re able to include all our devices in one protected mesh and get low-latency access anywhere – with none of the overhead of complex VPN or SD-WAN setups,” MacLeod notes.
For Dexory, Tailscale provided exactly what their cutting-edge robots needed behind the scenes: a networking solution as advanced and agile as the robots themselves. Dexory’s fleet stays securely connected and accessible, and the team can devote its energy to optimizing warehouse operations – confident that Tailscale is seamlessly handling the connectivity in the background.
Dexory’s case exemplifies how a modern Zero Trust network like Tailscale can transform edge connectivity. Autonomous robots, IoT devices, and cloud analytics all coexist on Dexory’s tailnet with minimal fuss. The result is a smarter, safer infrastructure: real-time warehouse intelligence delivered efficiently, and a global robotics network that simply runs – no strings (or cables) attached.